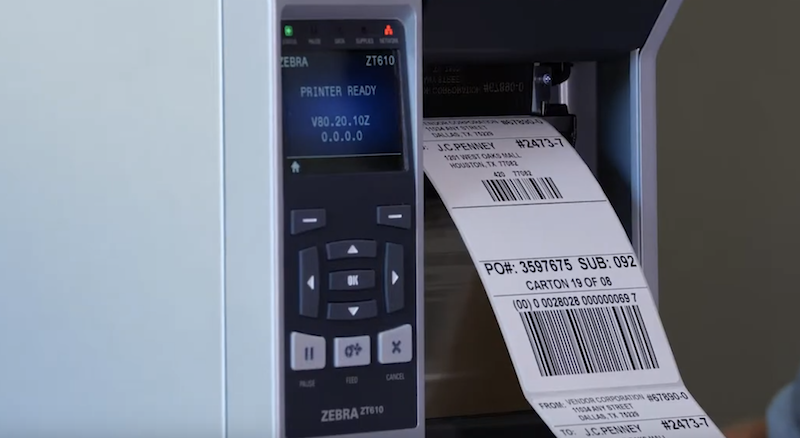
How Poor Labeling Can Wreak Havoc on a Business (Re-Labeling Scenarios)
Are you having barcoding issues related to incorrect data displaying? Are your scanners not properly reading your barcodes on your labels?
Barcodes are a simple technology that we’re all familiar with, but they really are “make or break.” Barcode printing and scanning issues can can cause supply chain logistical issues, product recalls, supplier bill backs, loss of customer trust, missed shipments, and hits to your brand reputation.
In one instance, a customer ordered a product from a vendor, but instead of receiving the product they asked for, because of poor labeling procedures, they received a bag of car parts and a soup ladle. And this is a lot more common than one might think.
Along with the initial application of a product label, there are multiple instances in which the label might have to be duplicated and re-affixed for one reason or another. Here are a few examples.
Label Duplication Common Scenarios
Re-boxing items.
When replacing a product box, the serial number must be printed and applied to the outside of the new box.
Buying in bulk and reselling individually.
If a barcode label is applied only to the outer box of 100 of the same item, when boxing as individual items, the number needs to be printed and applied.
Individually packaging smaller components.
Amazon requires that loose items must be bagged in a plastic bag (because it’s easier for stacking). They also require the barcode to be readable at all times. Since the hang tag on a shirt may move or turn over, the seller will scan the hang tag the duplicate label on the outside of the bag in the center, guaranteeing a good read.
Removing and re-barcoding the top sheet in a stack of items.
A manufacturer produces thin sheets of steel and stores them on pallets. Only the top sheet is barcoded which lets the users know the features of the material on the pallets. Because all the pallets on the floor have different material types and thicknesses that all look the same, the loss of the barcode would mean loss of control of the inventory, making the steel sheets worthless. To avoid this loss, the workers scan the barcode on the top sheet on a pallet before taking a sheet, then place the duplicated label on the next sheet in the pallet, keeping the steel sheets “known” and cutting down inventory “losses”
Medical testing and lab results.
In a lab the barcoded contact sheet shows information about a person getting a sample taken. All sample vials taken from that person are labeled with duplicate barcodes (scanned from the contact sheet).
Picking orders in a warehouse.
When picking orders in a warehouse, the picker will have a barcoded order sheet. Each time a product that is picked for that order, a duplicate label is created and placed on the picked item. When the order gets to shipping, all the codes are scanned on the products to be sure the right items are shipped with each order.
If the labeling process breaks down during any of these steps, business can grind to a halt. Customer orders will be delayed, vital medical records & samples will be lost, food recalls will become widespread as they can’t be properly tracked, whole stacks of product will go to waste, Amazon and other large sellers will ban you from selling on their platforms, and costs of doing business in general will skyrocket.
The next time you’re looking to upgrade your barcoding and labeling technology, don’t try the do-it-yourself method. Instead, seek the help of professionals who can look at your business needs, your labeling procedures, and your areas in need of improvement. Don’t leave this vital task up to chance.
Here at BarcodeDuplicator.com, we work closely with Seagull Scientific to offer BarTender software. This program will revolutionize the way you label your items, saving you time, money and lots of headaches. The best part? It can be up and running in a week or less.
Avoid Label Sheet Waste
Print only what you need; no more throwing away label sheets with only one label used. When you use sheets, there are multiple labels on a sheet. If you only want to print one label, only the top left label will be printed and the rest of the sheet is wasted. Money down the drain.
Speed & Efficiency
Zebra printers can print a 6" label in less than a second. Your laser jet is much slower.
Learn more by using the form below to get a customized quote.